محتوا
- ریخته گری تحت فشار قطعات باکیفیت و پیچیده را تولید میکند
- فرایند ریخته گری تحت فشار چیست؟
- بررسی فرایند ریخته گری تحت فشار
- ساخت قالب
- تزریق مواد مذاب
- جدا کردن قالب
- اصلاح و پرداخت قطعه
- مزایای فرایند ریخته گری تحت فشار
- امکان تولید قطعات با تیراژ بالا
- کیفیت بسیار بالای قطعات
- ضخامت بسیار پایین دیواره قطعه
- امکان ساخت قطعات پیچیده
- دوام و مقاومت بالای قالبها
- کاربردهای ریخته گری تحت فشار
- صنعت اتومبیلسازی
- صنعت پزشکی
- صنعت هوانوردی
- نکات مهم درباره ریخته گری تحت فشار
- دقت قطعات تولیدی با ریخته گری تحت فشار بسیار بالا است
- سوالات متداول
- آیا میتوان ریخته گری تحت فشار را برای فولاد استفاده کرد؟
- حداقل ضخامت دیواره که میتوان با روش ریخته گری تحت فشار به آن دست یافت چقدر است؟
- بهترین دما برای انجام فرایند ریخته گری تحت فشار چقدر است؟
- کیفیت پرداخت قطعات تولیدی به روش ریخته گری تحت فشار بیشتر است یا ریخته گری در فشار پایین؟
ریخته گری تحت فشار قطعات باکیفیت و پیچیده را تولید میکند
فرایند ریخته گری تحت فشار (HPDC) یکی از روشهای مرسوم برای تولید قطعات پیچیده است. با استفاده از این این تکنیک میتوان بلوک موتور اتومبیل و دیگر بخشهای پیچیده اتومبیل را به آسانی تولید کرد. علاوه بر این ابزارهای جراحی و بسیاری از قطعات حساس نیز با استفاده از ریخته گری تحت فشار تولید میشوند. فرایند ریخته گری تحت فشار بسیار تکنیکی است و انجام آن نیازمند تجهیزات ویژه است. بنابراین باید پیش از هر چیز با بررسی نیازها و امکانات بهترین شیوه را انتخاب کنید. در این مطلب با فرایند ریخته گری تحت فشار و جزئیات آن آشنا میشویم.
فرایند ریخته گری تحت فشار چیست؟
ریخته گری تحت فشار یکی فرایند تولید قطعه است که طی آن فلز مذاب به درون یک قالب منتقل میشود. انجام این پروسه تحت فشارهای بالا (فشارهای هیدرولیک) موجب انتقال بهتر فلز مذاب به درون قالب میشود. پس از سرد شدن و شکل گرفتن قطعه میتوان محصول نهایی را به راحتی خارج کرد. قالب مورد استفاده در این فرایند معمولا فولادی است و میتوان آن را بارها استفاده کرد.
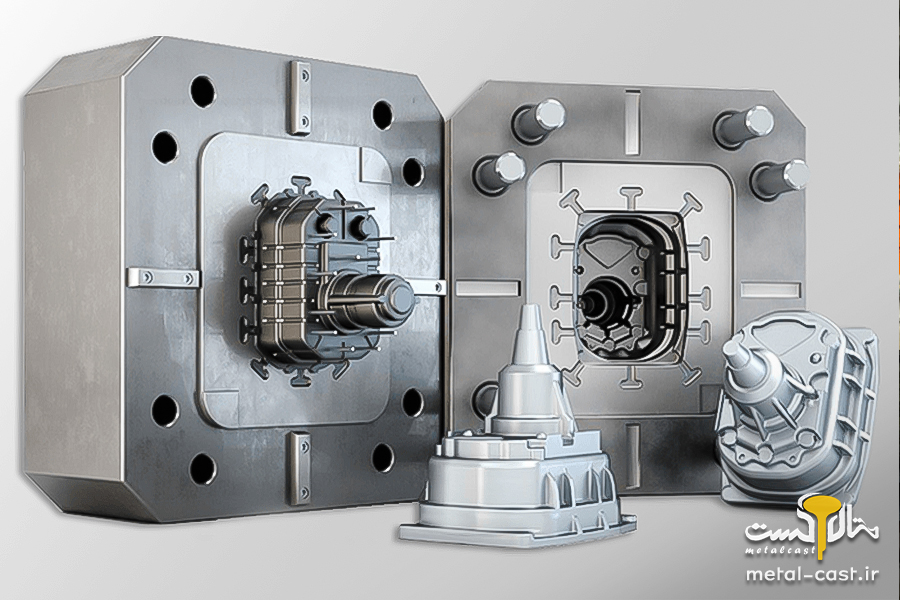
این پروسه اولین بار در اواسط قرن نوزدهم و با هدف تولید دستگاه تایپ به کار رفت. برای این منظور قالب کلیدهای دستگاه با دقت بالا طراحی میشدند. خیلی زود از این روش در دیگر بخشها نیز استفاده شد. از سال ۱۹۱۴ بعد صنایع از متریالهای جدید مانند آلیاژهای روی و آلومینیوم برای تولید قطعات استفاده کردند و بسیاری از محصولات با آنها ساخته شد. علاوه بر این امروزه بسیاری از قطعات آلیاژی پیچیده با روش ریخته گری تحت فشار تولید میشوند.
بررسی فرایند ریخته گری تحت فشار
فرایند ریخته گری تحت فشار از مراحل مشخص تشکیل میشود که باید با دقت کافی انجام شوند. در این پروسه فلز مذاب در فشار بسیار بالا به درون یک قالب ریخته میشود و پس از سرد شدن به صورت محصول نهایی خارج میشود. در ادامه با مراحل مختلف فرایند ریخته گری آشنا میشویم.
ساخت قالب
پیش از هر چیز باید قالب مناسب و با کیفیت برای ریخته گری ساخته شود. این مرحله نخست چرخه ریخته گری تحت فشار است و تا حد زیادی در هزینه تولید و ضایعات صرفهجویی خواهد کرد. در ادامه سطح داخلی قالب باید به خوبی روغنکاری شوند تا خروج قطعه از قالب تسهیل شود.

تزریق مواد مذاب
در این مرحله فلز مذاب از درون یک منفذ باریک به درون قالب تزریق میشود. تزریق مواد مذاب به دو صورت کلی سرد و گرم انجام میشود. تفاوت این دو مرحله در دمای ماده مذاب است و تاثیر مستقیم بر کیفیت قطعه میگذارد. این دو پروسه عبارتند از:
- محفظه تزریق داغ: در این روش سیستم تزریق فلز مذاب در یک کوره ادغام شده است. به این ترتیب ماده مذاب از طریق پیستون به یک نازل و سپس قالب منتقل میشود. از این روش میتوان برای ریخته گری تحت فشار روی، منیزیم و سرب استفاده کرد
- محفظه تزریق سرد: در تزریق با محفظه سرد فلز مذاب به صورت دستی یا توسط مکانیسم خودکار به یک محفظه مخصوص منتقل میشود. در ادامه با استفاده از نیروی هیدرولیک فلز مذاب به درون قالب تزریق خواهد شد. پس از سرد شدن فلز امکان باز کردن قالب و خارج کردن قطعه فرا میرسد. شما میتوانید از این پروسه برای ریخته گری تحت فشار فلزاتی که دمای ذوب بالا دارند استفاده کنید (آلومینیوم، برنج، منیزیم). شما میتوانید در این فرایند از تزریق افقی یا عمودی استفاده کنید
جدا کردن قالب
پس از آنکه مطمئن شدید تمام مواد مذاب درون قالب سرد شدهاند باید آن را خارج کنید. برای این منظور بخشهای جدا شونده بر روی قالب پیشبینی میشود تا بتوان قطعه را به راحتترین شکل ممکن جدا کرد. شما میتوانید به راحتی با استفاده از این قطعات متحرک قطعه را از درون قالب بیرون آورید.

اصلاح و پرداخت قطعه
آخرین گام در فرایند ریخته گری تحت فشار جدا کردن بخشهای اضافی و انجام اصلاحات لازم بر روی قطعه است. با انجام این کار صاحب محصول نهایی خواهید شد. ضایعات به دست آمده در این فرایند را میتوان دوباره استفاده کرد و دوباره برای ساخت قطعات جدید به کار برد.
مزایای فرایند ریخته گری تحت فشار
فرایند ریخته گری تحت فشار به دلیل داشتن مزایای بسیار زیاد محبوبیت بالایی دارد. شما میتوانید قطعات تولید شده به این روش را در صنایع مختلف مشاهده کنید. در ادامه با برخی از مهمترین مزایای فرایند ریخته گری تحت فشار آشنا میشویم.
امکان تولید قطعات با تیراژ بالا
شما میتوانید با استفاده از روش ریخته گری تحت فشار نرخ تولید قطعات را بالا ببرید. این تکنیک در مقایسه با ریخته گری در فشار کم یا ریخته گری گرانشی تیراژ بالاتری دارد. استفاده از روش ریخته گری تحت فشار به شما این امکان را میدهد تا فلز مذاب را با سرعت زیاد به درون قالب تزریق کنید و در زمان کوتاه قطعات گوناگون را بسازید. به همین دلیل از این پروسه برای تولید با حجم بالا استفاده میشود

کیفیت بسیار بالای قطعات
قطعات تولید شده با روش ریخته گری تحت فشار کیفیت ابعادی و پرداخت سطح عالی دارند. به همین دلیل قطعات نهایی به پرداخت و اصلاح کمتری نیاز دارند و همین موضوع موجب صرفهجویی در زمان و هزینهها خواهد شد. پرداخت خوب قطعات فرایند آبکاری را نیز آسانتر میکند. علاوه بر این مزایای فرایند ریخته گری تحت فشار موجب یکنواختی بسیار خوب و خواص مکانیکی بهینه قطعات تولیدی میشود.
ضخامت بسیار پایین دیواره قطعه
با انجام فرایند ریخته گری تحت فشار میتوانید قطعاتی با دیواره بسیار نازکتر در مقایسه با دیگر تکنیکها تولید کنید. به این ترتیب دست یافتن به ضخامت دیوار کمتر از ۰.۴۰ میلیمتر نیز امکانپذیر خواهد بود. این موضوع به سازندگان و صنعتکاران اجازه میدهد قطعات سبکتر و ظریفتر را تولید کنند. علاوه بر این میتوان پیچها و آسترها را در طول فرایند ریخته گری به قطعات اضافه کنید و از مراحل مونتاژ بکاهید.
امکان ساخت قطعات پیچیده
فرایند ریخته گری تحت فشار اجازه ساخت قطعات و حجمهای مختلف و پیچیده را میدهد. انعطافپذیری قطعات تولیدی در فرایند ریخته گری تحت فشار یکی از مهمترین دلایل محبوبیت این فرایند در صنایع مختلف است.
دوام و مقاومت بالای قالبها
قالبهای مورد استفاده در فرایند ریخته گری تحت فشار مقاومت بسیار بالایی دارند. به همین دلیل طول عمر آنها نیز بالا است و میتوانند بارها مورد استفاده قرار گیرند. امکان استفاده مجدد از قالب در هزینههای ریخته گری تحت فشار و قیمت تمام شده محصولات صرفهجویی میکند.

کاربردهای ریخته گری تحت فشار
ریخته گری تحت فشار به دلیل کیفیت بسیار بالای محصولات تولیدی کاربردهای بسیار گوناگون و متنوعی دارد. شما میتوانید با استفاده از پروسه HPDC انواع محصولات را برای صنایع مختلف تولید کنید. در ادامه با برخی از مهمترین کاربردهای ریخته گری تحت فشار آشنا میشویم.
صنعت اتومبیلسازی
با استفاده از ریخته گری تحت فشار میتوان انواع قطعات آلومینیومی و منیزیمی مورد نیاز صنعت خودروسازی را تولید کرد. این قطعات در بخشهای مختلف اتومبیل مانند بلوک موتور، جعبه دنده، سیستم انتقال روغن، دهانه موتور و بخشهای ساختاری دیگر مانند چارچوب بدنه نصب و استفاده میشوند.
صنعت پزشکی
تکنیک ریخته گری تحت فشار برای تولید قطعات پزشکی بسیار سبک وزن و بادوام استفاده میشود. این روش پیشرفته را برای تولید تجهیزات پزشکی در تیراژ بالا به کار میبرند. تجهیزات چشمپزشکی، تجهیزات دندانپزشکی مانند سرنگهای فلزی و … با استفاده از فرایند HPDC تولید میشوند. در جدول زیر برخی از تجهیزات پزشکی که به روش ریخته گری تحت فشار تولید میشوند را مشاهده میکنید.
اسکنرهای MRI | اسکنرهای CT | تجهیزات فراصوت |
مانیتورها | تجهیزات نور و روشنایی | تجهیزات تشخیصی |
لوازم دندانپزشکی | تجهیزات اتاق عمل و جراحی | سرنگهای فلزی |
صنعت هوانوردی
روش ریخته گری تحت فشار به دلیل امکان قالبگیری قطعات پیچیده و با حجمهای خاص به منظور ساخت قطعات مختلف صنعت هوافضا و هوانوردی کاربرد دارد. با استفاده از این تکنیک میتوانید بخشهای مختلف را با دقت و کیفیت بسیار بالا تولید کنید. بسیاری از این قطعات با استفاده از آلیاژ آلومینیوم، روی و منگنز تولید میشوند و از آنها در موتور و قطعات مختلف بدنه هواپیما استفاده میکنند.
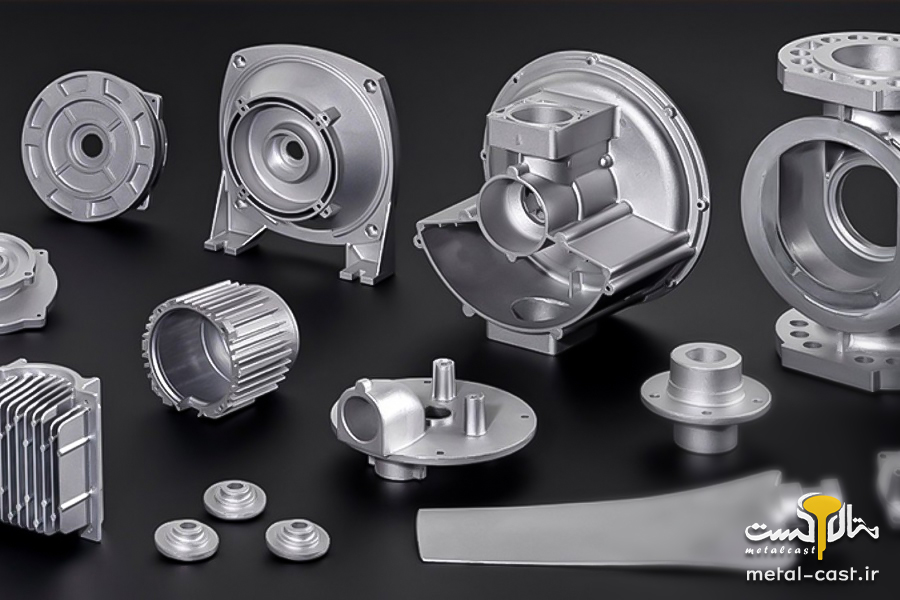
نکات مهم درباره ریخته گری تحت فشار
پروسه ریخته گری تحت فشار امکان تولید قطعات را در شرایط خاص میدهد. شما برای انجام این تکنیک پرکاربرد باید برخی نکات و الزامات را مدنظر قرار دهید. در ادامه با برخی از مهمترین نکات درباره ریخته گری تحت فشار آشنا میشویم.
- فلز و آلیاژهای منیزیم را میتوان به دو صورت داغ و سرد ریخته گری تحت فشار کرد
- معمولا قطعات کوچک و پیچیده به روش تزریق داغ ریخته گری میشوند
- فلز روی پس از ریخته گری تحت فشار دوام بیشتری در مقایسه با قطعات آلومینیومی دارد
- انجام فرایند تزریق و ریخته گری تحت فشار تنها چند ثانیه زمان میبرد
- قالبهای مورد استفاده در ریخته گری تحت فشار باید کاملا ایزوله و بدون هرگونه محفظ باشند
- معمولا این تکنیک ریخته گری در فشار ۱,۵۰۰ تا ۲۵,۰۰۰ پوند بر اینچ (PSI) انجام میشود
- هزینه ریخته گری تحت فشار در مقایسه با دیگر روشها کمتر است
- تولید با تیراژ بالا هزینههای پرداختی برای تهیه قالبهای با کیفیت و گرانقیمت را جبران میکند
- ریخته گری فشرده با ترکیب ریخته گری پرفشار و کمفشار انجام میشود و میـواند تمام گازهای مزاحم که موجب تخریب قطعات میشوند را از بین ببرد و جریان ثابت مذاب را وارد قالب کند

دقت قطعات تولیدی با ریخته گری تحت فشار بسیار بالا است
در فرایند ریخته گری HPDC فلزات مذاب با فشار بسیار بالا به درون قالبهای بسیار مقاوم وارد میشوند. این فشار در بیشتر موارد با استفاده از دستگاههای هیدرولیک ایجاد میشود و تا زمان انجماد کامل قطعات باقی میماند. پس از سرد شدن مواد و شکل گرفتن قطعه نهایی میتوانید قالب را باز کنید و محصول مدنظر را از آن بیرون آورید. در پایان قالب را میتوان برای تولید دوباره قطعات استفاده کرد.
مزایای بسیار زیاد این تکنیک مانند تیراژ بالای تولید، پرداخت نهایی عالی و امکان ساخت قطعات پیچیده و متنوع باعث میشوند تا ریخته گری تحت فشار به صورت گسترده در صنایع مختلف استفاده شود. مجموعه متالکست یک سامانه آنلاین برای دریافت سفارشهای ریخته گری است. شما میتوانید با استفاده از خدمات ما انواع قطعات را با کیفیت بسیار بالا تولید کنید.
سوالات متداول
آیا میتوان ریخته گری تحت فشار را برای فولاد استفاده کرد؟
بله، شما میتوانید فولاد را به روش تحت فشار ریخته گری کنید. هرچند چالشهای تولید قطعات با فولاد بیشتر از دیگر فلزات مانند آلومینیوم یا روی است، اما میتوان با استفاده از تجهیزات خاص این پروسه را انجام داد.
حداقل ضخامت دیواره که میتوان با روش ریخته گری تحت فشار به آن دست یافت چقدر است؟
شما میتوانید با استفاده از روش ریخته گری تحت فشار ضخامت دیواره قطعه را به ۱ تا ۲.۵ میلیمتر برسانید. علاوه بر این سطح قطعه نهایی بسیار صاف و یکدست خواهد بود و دوام بسیار بالایی دارد.
بهترین دما برای انجام فرایند ریخته گری تحت فشار چقدر است؟
بهترین دما برای انجام ریخته گری تحت فشار بین ۱۵۰ تا ۳۰۰ درجه سانتیگراد است. در صورتی که دمای ذوب بیشتر از این مقدار باشد احتمال ایجاد حباب، جوش و انقباض قطعه افزایش پیدا میکند. برای انجام بهتر فرایند ریخته گری باید قالب پیش از ورود مواد مذاب گرم شود.
کیفیت پرداخت قطعات تولیدی به روش ریخته گری تحت فشار بیشتر است یا ریخته گری در فشار پایین؟
به طور کلی فرایند ریخته گری LPDC در فشار پایین در فشار ۰.۰۸ تا ۰.۱۵ مگاپاسکال انجام میشود، در حالی که ریخته گری HPDC به فشارهای ۳۰ تا ۷۰ مگاپاسکال نیاز دارد. محصول نهایی فرایند پرفشار دارای پرداخت عالی است، اما در پروسه کمفشار پرداخت قطعه نهایی کاملا معمولی خواهد بود.