ریخته گری فلز شامل ریختن فلز مذاب در حفره قالب، سپس سرد و جامد شدن قالب و فلز و در نهایت خارج کردن قطعه است. تمام فلزات اصلی قابلیت ریخته گری دارند که آهن، آلومینیوم، منیزیم، روی، فولاد و آلیاژهای مس رایجترین آنها هستند.
انواع روش های ریخته گری را میتوان بر اساس مکانیزم تولید به چند نوعِ ریخته گری ماسهای، دایکاست، پیوسته، ریخته گری خلأ، سانتریفیوژ، ریخته گری کمفشار و… تقسیم کرد.
این روشها برای ساخت طیف وسیعی از وسایل؛ از قطعات کوچک و ساده گرفته تا قطعات پیچیده ماشینآلات و در صنایع مختلفی همچون پزشکی، خودروسازی، هوافضا و غیره کاربرد دارند. در ادامه این مقاله با ما همراه باشید تا جزئیات بیشتری در این مورد یاد بگیرید. اگر شما صنعتگر یا به دنبال تولید قطعه مدنظر خود هستید میتوانید از کارگاه ریخته گری ما در متالکست استفاده کنید.

انواع روش های ریخته گری چیست؟
برای پاسخ به این سوال، باید گفت انواع مختلفی از فرآیندهای ریخته گری وجود دارد و هر روش راهکار منحصربهفردی در اختیار صنایع مختلف قرار میدهد و درعینحال مزایا و معایب خاص خود را نیز دارد.
بهطورکلی میتوان همه روشهای ریخته گری را بر ۲ پایه نامگذاری کرد که در ادامه مفصل به آن خواهیم پرداخت:
- انواع روشها بر اساس مکانیزم انجام
- انواع روشها بر اساس مواد و فلزات
انواع روش ریخته گری بر اساس مکانیزم انجام
در مقاله ریخته گری چیست به طور مفصل درباره این صنعت حرف زدیم و انواع روشهای آن را تعریف کردیم. همچنین گفتیم که روشهای مختلفی برای ریختهگری فلزات وجود دارد که بر اساس مکانیزم انجام آنها به دستههای زیر تقسیم میشوند:
- ریخته گری ماسهای
- ریخته گری دقیق
- دایکاست
- ریخته گری سانتریفیوژ
- ریخته گری گرانشی
- ریخته گری خلا
- ریخته گری کمفشار
- ریخته گری لاست فوم
- ریخته گری پیوسته
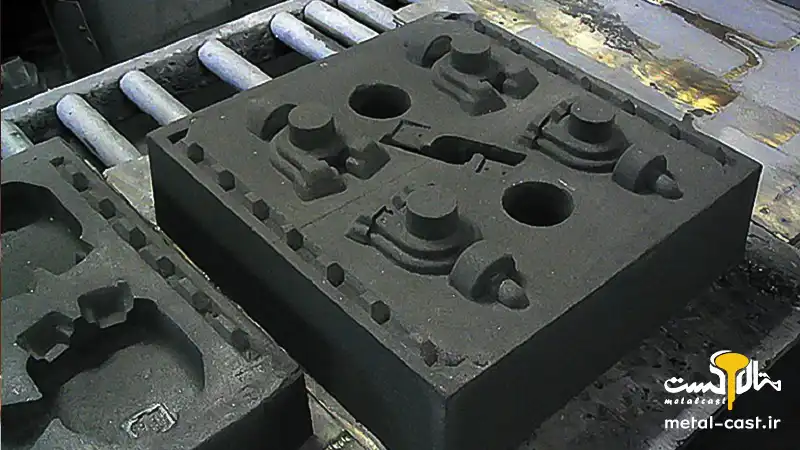
ریخته گری ماسهای
در مقاله ریخته گری ماسه ای گفتیم که این نوع ریخته گری یک روش همهکاره برای شکلدهی فلزات است و جهت تولید قطعات ریختگی فلزی پیچیده، از قالبهای شنی غیر قابل استفاده مجدد استفاده میکند. این تکنیک در بسیاری از صنایع مختلف دیده میشود؛ زیرا در شکل دادن به آلیاژهایی با دمای ذوب بالا مانند فولاد، نیکل و تیتانیوم نسبت به سایر روشها برتری قابلتوجهی دارد.
مراحل انجام ریخته گری ماسهای عبارتاند از:
- الگوسازی
- ساخت قالب
- مرحله بستن دو نیمه قالب Cope و Drag
- ریختن فلز مذاب در دمای
- سرد شدن و انجماد فلز مذاب
- برداشتن قالب بعد از سپری شدن دوره انجماد
- تمیز کردن و جدا کردن بخشهایی که به قطعه اصلی متصل هستند

ریخته گری دقیق
در روش ریخته گری دقیق، یک موم یا الگوی پلیمری مناسب با فرو بردن در دوغاب مواد نسوز پوشش داده میشود. هنگامی که پوشش مواد نسوز سفت شد و اصطلاحا خودش را گرفت، فرآیند غوطهوری دوباره چندین بار تکرار میشود تا ضخامت و استحکام پوشش افزایش پیدا کند. هنگامی که پوشش نهایی به اندازه کافی سخت شد، موم ذوب میشود و فلز مذاب در حفرهای که توسط الگوی مومی ایجاد شده است، ریخته میشود و در نهایت پس از ریختن فلز در داخل قالب، با شکستن قالب نسوز قطعه ریخته گری خارج میگردد.
انواع آلیاژهایی که میتوان با ریخته گری دقیق تولید کرد عبارتاند از فولاد کربنی، فولاد آلیاژی، آلیاژهای مقاوم در برابر حرارت، فولاد ضدزنگ، آلیاژهای دقیق، آلیاژهای آهنربای دائمی، آلیاژهای بلبرینگ، آلیاژهای مس، آلیاژهای آلومینیوم، آلیاژهای تیتانیوم و چدن شکلپذیر و غیره.

دایکاست؛ روشی عمده برای ریخته گری
دایکاست یک فرآیند ریختهگری دائمی است که در آن فلز مذاب با فشارهای بین ۰.۷ تا ۷۰۰ مگاپاسکال وارد قالب شده و سپس منجمد میگردد. از دایکاست معمولا بهعنوان ریخته گری تحت فشار نیز نام برده میشود و در محفظههای خودرو، قطعات لوازمخانگی و اسباببازیها مورد استفاده قرار میگیرد.
در دایکاست، فلزات غیرآهنی مانند آلومینیوم، روی، مس، منیزیم، سرب و همینطور آلیاژهای قلع، به طور گسترده برای تولید اجزای پیچیده با کیفیت بالا استفاده میشوند. عناصر شیمیایی مختلفی نیز به فلز مذاب اضافه میشوند تا به ترکیب شیمیایی فلز مورد نظر دست یابند و بتوانند برخی از الزامات چالشبرانگیز را برآورده سازند. برای مطالعه بیشتری در مورد این روش بهتر است مقاله ریخته گری دایکاست را مطالعه کنید.
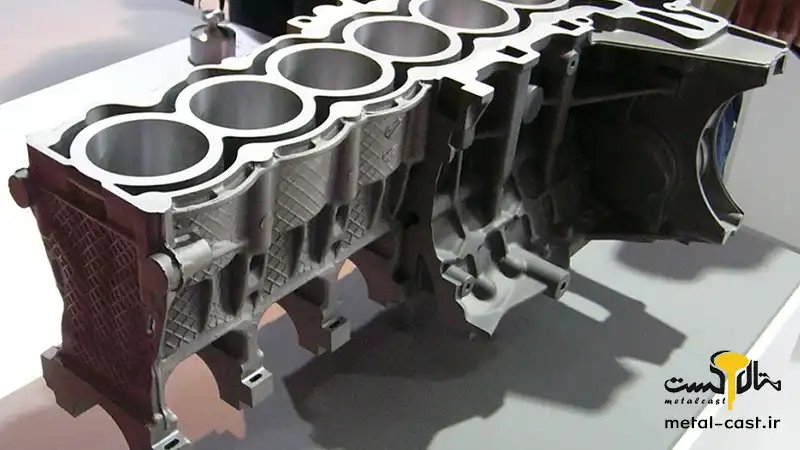
ریخته گری سانتریفیوژ؛ یکی از بهترین روش های ریخته گری
ریخته گری سانتریفیوژ یا گریز از مرکز، به چندین تکنیک ریخته گری اشاره دارد که برای توزیع فلز مذاب در نواحی بیرونی یک حفره دایرهای قالب، از نیروهای گریز استفاده میکنند. این فناوری در اوایل دهه ۱۸۰۰ پدیدار شد و در مقایسه با سایر فرآیندهای تولید مانند آهنگری، میتواند برای ایجاد قطعات پیچیده یک روش مقرونبهصرفه باشد.

ریخته گری گرانشی؛ روشی برای ریخته گری فلزات غیرآهنی
ریخته گری گرانشی نوعی ریختهگری دایکاست است و برای قطعات آلیاژی غیرآهنی کاربرد دارد. این روش گاهی اوقات ریخته گری با قالب دائمی نیز نامیده میشود و معمولا برای آلیاژهای آلومینیوم، روی و مس قابل استفاده است. این فرایند برای پر کردن قالب با فلز مذاب از نیروی گرانش استفاده میکند و قطعات دقیق و پیچیده با پرداختهای سطحی با کیفیت بالا در اختیار شما قرار میدهد.

ریخته گری خلأ؛ ریخته گری با قالب سیلیکونی
روش ریخته گری خلا که گاهی ریخته گری اورتان یا ریخته گری پلییورتان نیز نامیده میشود، برای ساخت قطعات پلاستیکی و لاستیکی تحت خلا از قالبهای سیلیکونی استفاده میکند. باید گفت ریخته گری خلا یک فرآیند تولیدی بسیار سازگار است و میتواند برای تولید قطعات پیچیده در رزینهای پلی اورتان و نایلون ریخته گری از فرایند قالبگیری تزریقی تقلید کند. مشخصات کلی ریخته گری خلا در جدول زیر آورده شدهاند:
زمان تولید | ظرف ۲۴ ساعت (۵ روز کاری برای حداکثر ۳۰ تا ۵۰ قطعه) |
انتخاب مواد | امکان انتخاب طیف گستردهای از مواد |
دقت | ۰.۳%± (با در نظر گرفتن حد پایینی تلرانس برای ابعاد کوچکتر از ۱۰۰ میلیمتر) |
کمترین ضخامت دیواره | برای اطمینان از پر شدن مناسب قالب، ضخامت دیواره باید حداقل ۰.۷۵ باشد. اما بهترین نتایج با ضخامت دیواره ۱.۵ میلیمتر به دست میآید |
بیشترین ابعاد قطعه | عامل محدود کننده اندازه قالب، ابعاد محفظه خلا است |
تیراژ معمول | حداکثر ۵۰ قطعه در هر قالب |
ساختار سطح | سطح براق تا مات |
ریخته گری کمفشار؛ یکی روش های رایج برای ریخته گری آلومینیوم
ریخته گری کمفشار رایجترین فناوری برای ریخته گری آلیاژهای آلومینیوم است. این روش ریخته گری با داشتن قابلیتهای چشمگیر، این به ویژه در بهبود استحکام قطعات و عملکرد کلی آنها نقش مهمی بازی میکند. در این روش ریخته گری، فلز مذاب در قالب تحت فشار نسبتا کم (زیر ۰.۸ بار) قرار میگیرد. این تکنیک به ویژه برای ایجاد قطعات ریخته گری با کیفیت بالا همراه با خواص مکانیکی بهبودیافته مفید است.
ریخته گری لاست فوم؛ روشی نوین در ذوب فلزات و آلیاژها
ریختهگری لاست فوم یا فوم فداشونده یک نوآوری نسبتا جدید است که مزایای ریختهگری دقیق و ریختهگری ماسهای را با یکدیگر ترکیب میکند. در واقع ریخته گری لاست فوم شکلی از ریخته گری الگوی تبخیری است که در آن الگو به جای موم، از فوم ساخته میشود. الگوی فوم مانند ریخته گری دقیق با استفاده از مواد نسوز پوشانده میشود؛ اما پوسته توسط ماسه غیرفشرده احاطه میگردد تا به آن استحکام بخشد. هنگامی که فلز مذاب در پوسته ریخته میشود، الگوی فوم در تماس با آن بخار میشود. نتیجه فرآیندی است که کیفیت و دقت ریختهگری دقیق را با هزینههای کمتر و انعطافپذیری بیشتر ریختهگری ماسهای ترکیب میکند.
ریخته گری پیوسته؛ برای تولید محصولات نیمهتمام
ریخته گری پیوسته به طور گسترده برای فلزات و آلیاژهای غیرآهنی استفاده میشود. این فرایند ریخته گری در تامین مواد خام برای سایر فرآیندهای تولیدی از جمله نورد، آهنگری و اکستروژن نقش بسیار مهمی بازی میکند. در این روش ریختهگری قطعاتی با سطح مقطع ثابت تولید میشوند. در این فرآیند، فلز مذاب وارد قالب میشود. سپس فلز درحالیکه به طور مداوم در قالب کشیده یا فشار داده میشود، منجمد میگردد.
انواع روش ریختهگری بر اساس فلزات و آلیاژهای به کار رفته
انتخاب روش ریختهگری مناسب علاوه بر مکانیزم انجام؛ به عوامل مختلفی از جمله نوع فلز یا آلیاژ مورد استفاده بستگی دارد. بهطورکلی میتوان روشهای ریختهگری را بر اساس فلزات و آلیاژهای رایج به صورت زیر دستهبندی کرد:
- ریختهگری آلومینیوم:
آلومینیوم به دلیل سیالیت بالا، چگالی کم و قابلیت بازیافت به طور گسترده در ریختهگری استفاده میشود. روشهای رایج برای ریختهگری آلومینیوم را در مکانیزمهای بالا توضیح دادیم.
- ریختهگری در قالب ماسهای
- ریختهگری تحت فشار
- ریختهگری دایکاست
- ریختهگری با قالب دائمی
۲. ریختهگری چدن:
چدن به دلیل استحکام بالا، مقاومت در برابر سایش و قیمت مناسب، کاربردهای زیادی از جمله ساخت بلوک موتور، لولهها و شیرآلات دارد. روشهای رایج برای ریختهگری چدن عبارتاند از:
- ریختهگری در قالب ماسهای
- ریختهگری در قالب دائمی
- ریخته گری گریز از مرکز که در این مقاله به طور کامل توضیح دادیم.
۳. ریختهگری فولاد:
برای فولاد بهخاطر استحکام و چقرمگی بالایی که میتوان کاربردهای مختلفی از جمله ساخت ابزار، ماشینآلات و سازهها در نظر گرفت. روشهای رایج برای ریختهگری فولاد نیز عبارتاند از:
- ریختهگری در قالب ماسهای
- ریختهگری در قالبهای سرمایهای
- ریختهگری با روشهای دقیق
۴. ریختهگری سایر فلزات و آلیاژها:
علاوه بر فلزات و آلیاژهای ذکر شده، از روشهای ریختهگری برای تولید قطعاتی از جنس مس، برنج، منیزیم، نیکل و آلیاژهای خاص نیز استفاده میشود. لازم است بدانید که روش مناسب برای ریختهگری هر فلز یا آلیاژ به ویژگیهای خاص آن و کاربرد مورد نظر بستگی دارد.
در نهایت نیز عواملی مانند نوع فلز یا آلیاژ، هندسه قطعه، دقت ابعادی مورد نظر، کیفیت سطح و هزینه تولید تعیینکنندهی مناسبترین روش ریخته گری خواهند بود.
گذری به سایر روش های رایج ریخته گری
علاوه بر موارد گفته شده، روشهای دیگری نیز وجود دارد که برای ترکیب قطعات و ایجاد اتصال بین اجسامی که توسط سایر روشهای ریخته گری تولید شدهاند، به کار میروند:
- ریخته گری خوشهای: ریختهگری خوشهای یا ریختهگری چندتکهای (Cluster Casting) روشی برای تولید قطعات پیچیده از جنس فلزات و آلیاژها با اتصال چندین قطعه ریختهگری شده مجزا به یکدیگر است. این روش به طور گسترده در صنایع مختلف از جمله هوافضا، خودروسازی و ماشینآلات استفاده میشود.
- ریخته گری چاپی: ریختهگری چاپی یا ساخت افزودنی ریختهگری (Additive Manufacturing Casting) روشی نوین برای تولید قطعات فلزی از طریق ترکیب تکنولوژی چاپ سهبعدی و فرآیندهای ریختهگری سنتی است. در این روش، به جای استفاده از قالبهای معمولی، از مدلهای سهبعدی دیجیتال برای ساخت قالبهای سفارشی و تولید قطعات با هندسههای پیچیده و ظریف استفاده میشود.
- ریخته گری شمعی: ریختهگری شمعی یکی از روشهای ریختهگری فلزات است که در آن از یک مدل مومی به جای قالب استفاده میشود. این روش برای تولید قطعات توخالی و پیچیده با ظرافت و جزئیات بالا مناسب است.
- ریخته گری انجمادی: ریختهگری انجمادی یا انجماد جهتدار (Directional Solidification Casting) روشی برای تولید قطعات فلزی با ساختار دانهای ریز و یکنواخت و خواص مکانیکی مطلوب است. در این روش، فلز مذاب به طور کنترل شده در قالب ریخته میشود بهگونهای که جبهه انجماد از یک جهت خاص به سمت جهت دیگر حرکت کند.
متالکست؛ متخصص در انواع روش های ریخته گری
در این مطلب به معرفی انواع روش های ریخته گری پرداختیم که هر یک در کاربردهای خاصی مورد استفاده قرار میگیرد. شاید شما به دنبال یافتن بهترین روش ریخته گری باشید. اما بنا بر تجربه شخصی من، بهترین روش برای انتخاب ریخته گری، در مرحله طراحی انجام میشود که هزینه نسبتا پایینی دارد.
طراحی معمولا ۵ درصد یا حتی کمتر از هزینه محصول را شامل میشود. اما همین ۵ درصد میتواند ۷۰ تا ۸۰ درصد از هزینه محصول نهایی را تحت تاثیر قرار دهد. بنابراین، توصیه من این است که در هنگام تصمیمگیری برای انتخاب فرآیند ریختهگری فلز، بررسیهای لازم را انجام دهید و سپس مزایا و محدودیتهای هر روش را نیز مدنظر داشته باشید.
متالکست سامانه ثبت و پذیرش سفارشهای ریخته گری، انجام خدمات مدلسازی، ریخته گری چدن، فولاد و استیل در ایران است. ما در متالکست به شما صنعتگران محترم کمک میکنیم تا ضمن ثبت سفارشات ریخته گری قطعات صنعتی مورد خود به صورت آنلاین، از حسن انجام کار و کیفیت عالی و تضمینی قطعات اطمینان حاصل کنید.
سوالات متداول
معمولا از انواع روش های ریخته گری برای ساخت بلوکهای موتور خودرو، میل لنگ، تیغههای توربین، مجسمههای فلزی و چرخدندهها و سایر قطعات در صنایع گوناگون استفاده میشود.
ریخته گری دقیق و دایکاست از دقت ابعادی بسیار بالایی برخوردار هستند.
از میان مزایای ریخته گری کمفشار میتوان به حداقل سرباره و تخلخل و همچنین خواص مکانیکی مطلوب قطعه نهایی اشاره کرد.
پستهای مرتبط:
- انواع کورههای ریخته گری | روشهای مختلف برای ذوب کردن فلزات
- ریخته گری چیست؟ آشنایی با مراحل، انواع و کاربردها
- ریخته گری فلزات | روشی پرکاربرد و با دقت بالا برای ساخت انواع قطعات
- ریخته گری برنز | فرایندی برای تولید انواع محصولات و قطعات تزئینی و صنعتی
- همه چیز درباره ریخته گری فولاد: از اصول اولیه تا کاربردها